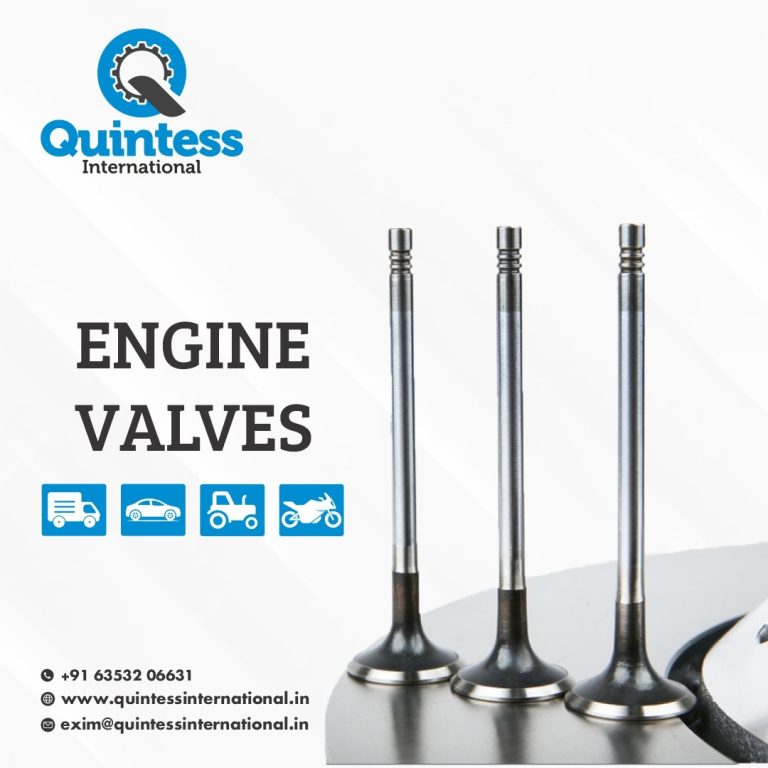
Quintess International is, indeed, a globally recognized name in the manufacturing and export of high-quality engine components. Specifically, their specialization includes engine valves, valve guides, and valve seats. Furthermore, with a footprint in over 25 countries, the brand has, consequently, established itself as a reliable provider of engine parts for a wide range of industries, including automobiles, trucks, buses, tractors, and earth-moving equipment.
International Reach and Global Presence
The company’s products are not only known for their durability and precision, but also making them a popular choice among OEMs and aftermarket customers worldwide. Additionally, their engine components, such as inlet and exhaust valves, are used in some of the most prestigious engine brands across various sectors, ranging from heavy-duty diesel engines for trucks to agricultural machinery and automotive cars.
Furthermore, with active exports to major regions like the United States, Europe, Latin America, the Middle East, and South East Asia, Quintess International continues to build on its reputation for quality and innovation.
Diverse Product Range
Quintess International offers a broad spectrum of products, catering to a variety of engine needs. Their product range includes:
- Inlet and Exhaust Valves for trucks, buses, and earth-moving machinery.
- Valves for automotive cars, industrial and agricultural engines.
- Products for two- and three-wheelers as well as generator sets.
Trusted by Top Engine Brands
Their high-quality components are regularly used by some of the most reputable engine manufacturers in the world. Among the well-known brands listed are:
- Automotive giants like BMW, Ford, Honda, and Volkswagen.
- Heavy machinery manufacturers such as Caterpillar, John Deere, and Komatsu.
- Agricultural equipment leaders like Mahindra and Fiat.
This wide-ranging applicability across various sectors highlights the versatility and reliability of Quintess International’s product offerings.
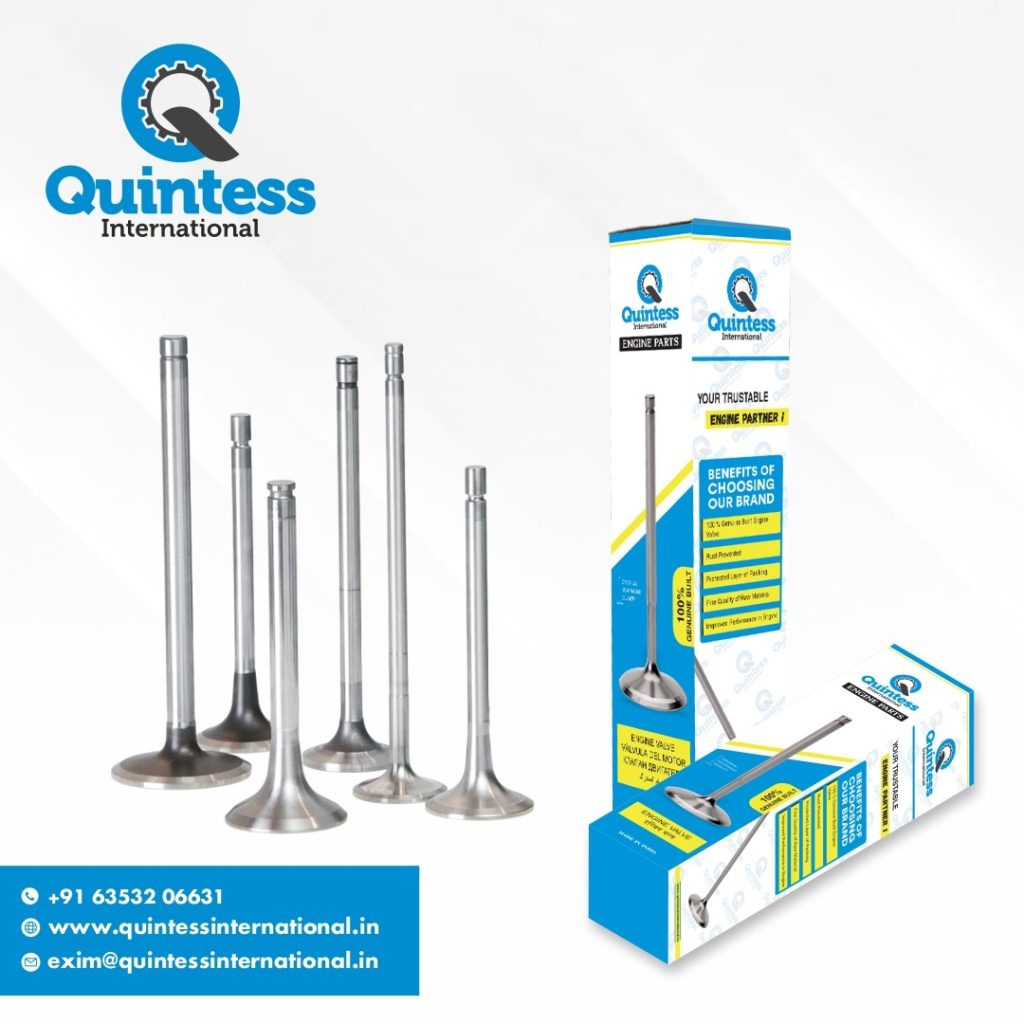
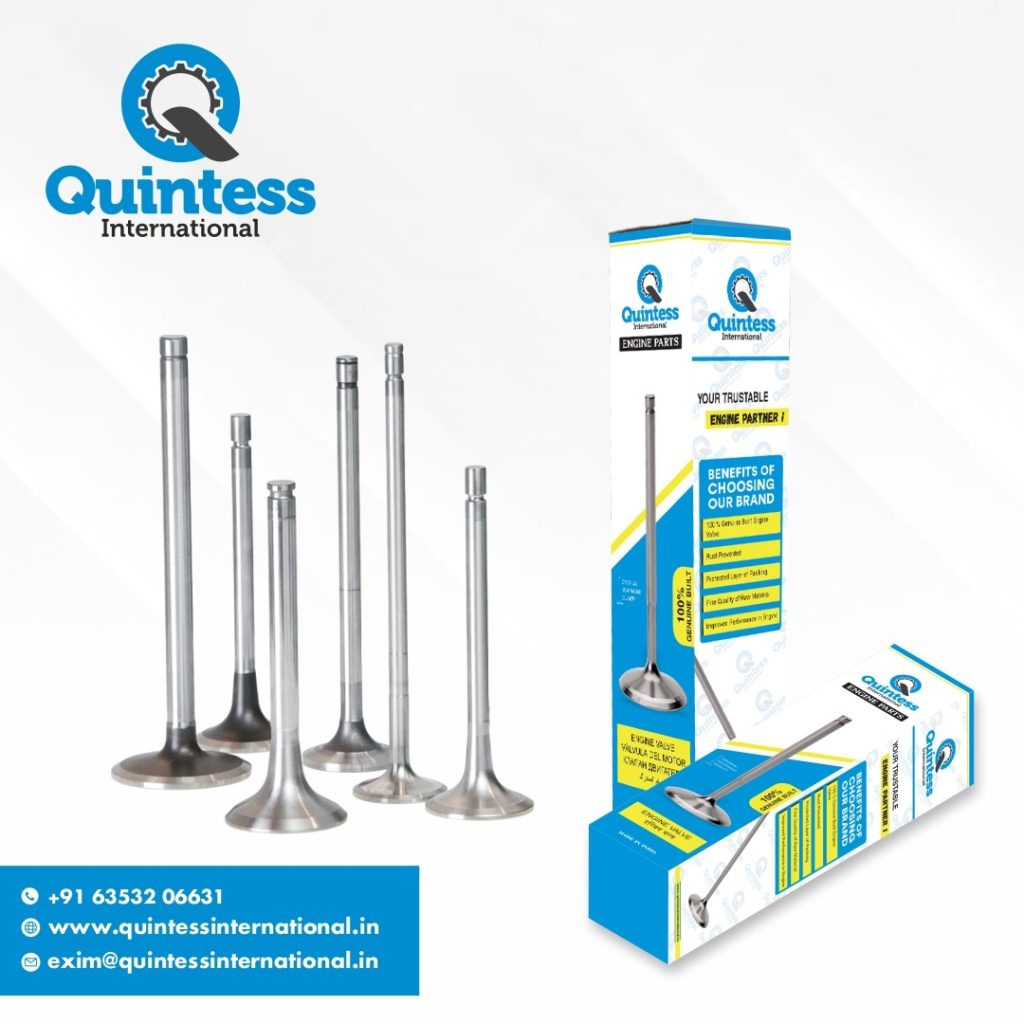
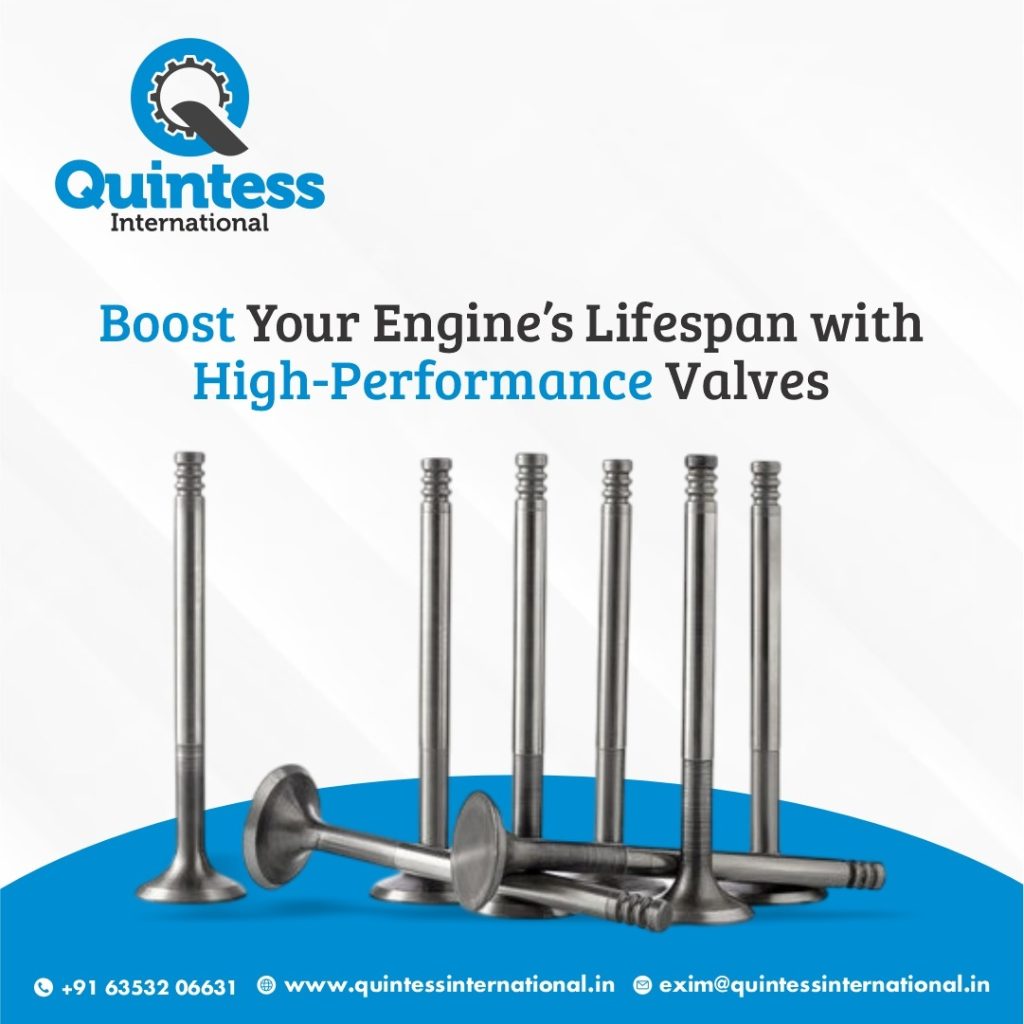
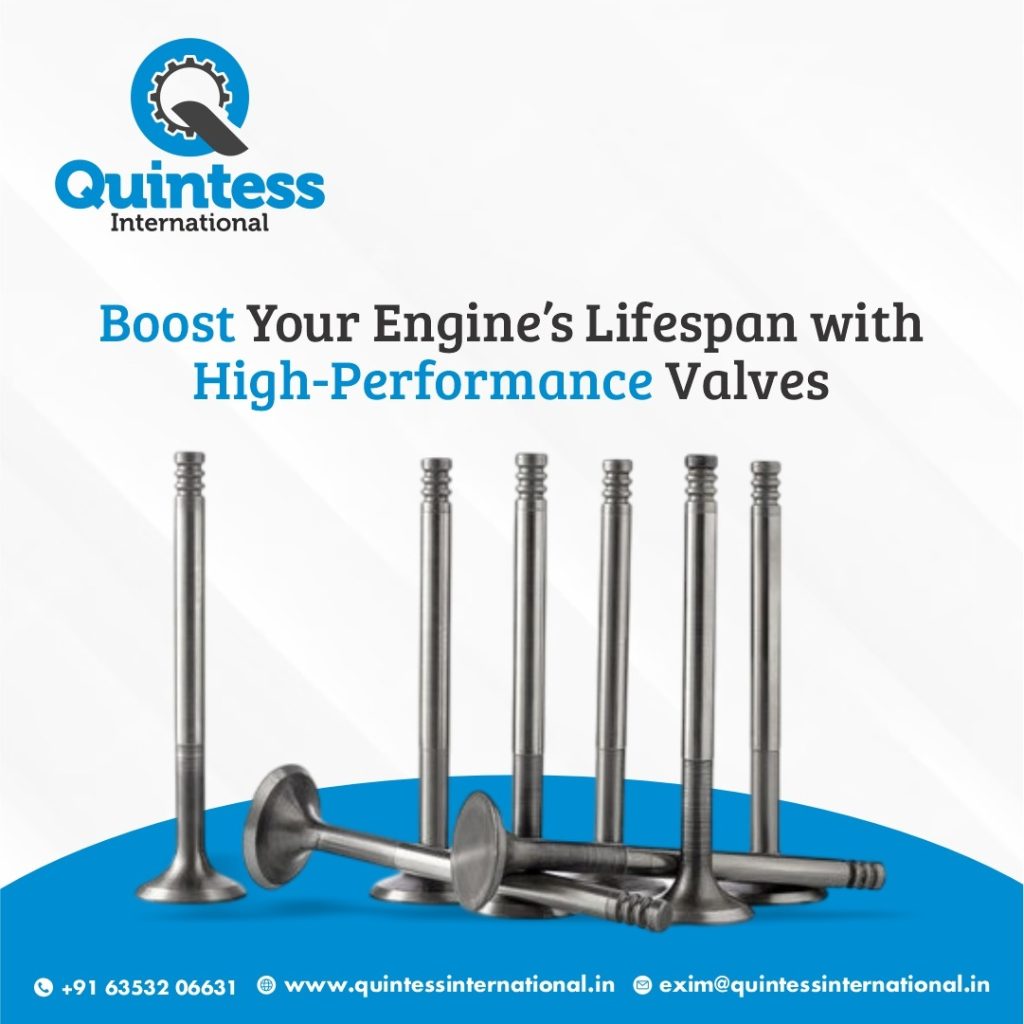
High performance designs and materials
Innovative designs are a key focus for achieving better engine performance, especially for high-speed and high-temperature applications like racing, aerospace, or heavy-duty industrial engines.
Variable Valve Timing (VVT): VVT technology adjusts the timing of valve opening and closing based on the engine’s speed and load conditions. This results in optimized performance, fuel efficiency, and reduced emissions. Variants like Dual VVT (adjusting both intake and exhaust valves) and Continuously Variable Valve Timing (CVVT) are common in high-performance engines.
Multi-Valve Systems: Using more than two valves per cylinder (e.g., four valves – two intake and two exhaust) allows for better airflow, resulting in improved combustion efficiency, higher power output, and better fuel economy. Multi-valve designs are standard in high-performance vehicles.
Camless Valves: Camless valve systems, like Freevalve developed by Koenigsegg, eliminate the traditional camshaft mechanism and allow electronic control of the valves. This system improves precision, reduces weight, and enhances engine performance by allowing independent control of valve timing, duration, and lift for each valve.
Sodium-Filled Valves: To cope with the high heat generated in high-performance engines, some valves (especially exhaust valves) are hollowed out and filled with sodium, which helps conduct heat away from the valve head, increasing durability and preventing warping under extreme conditions.
Coatings and Surface Treatments: Advanced coatings such as Diamond-Like Carbon (DLC) and Thermal Barrier Coatings (TBC) are applied to valve surfaces to reduce friction and wear, resist high temperatures, and improve heat dissipation. These coatings enhance longevity and allow for higher engine performance without damage.
Valve Materials
Titanium: Titanium valves are popular in high-performance and racing engines due to their lightweight nature and high strength-to-weight ratio. Their reduced weight allows for quicker opening and closing of valves, which improves engine response and allows for higher RPMs. Titanium also has excellent heat resistance, but it requires special coatings to prevent galling and wear.
Nickel-Based Superalloys (e.g., Inconel): Nickel-based alloys are commonly used for exhaust valves in high-performance engines because they can withstand extremely high temperatures (up to 1,000°C) without losing strength. These materials are highly resistant to corrosion and thermal fatigue, making them ideal for high-stress environments like aerospace and heavy-duty applications.
Steel Alloys: Advanced stainless steel alloys such as AISI 21-4N and AISI 23-8N are often used for valves in performance applications due to their high tensile strength, corrosion resistance, and ability to retain strength at high temperatures. For exhaust valves, martensitic stainless steels, which contain chromium and nickel, are common for their heat resistance.
Beryllium-Copper Alloys: These materials are used in high-performance engines for their ability to maintain strength and hardness under extreme conditions. Beryllium copper alloys are sometimes used for valve seats to prevent wear and ensure a tight seal at high temperatures.
Hollow-Stem Valves: To reduce weight without sacrificing strength, some valves are designed with hollow stems. This reduces the valve’s inertia, allowing for faster valve action, and can be combined with sodium filling for better heat dissipation.
Ceramic Valves: Though not widely used due to cost, ceramic valves are under development for extreme high-performance applications. Ceramics offer exceptional heat resistance, corrosion resistance, and low density, which makes them ideal for high-temperature environments, but they are brittle and require advanced manufacturing techniques.